Within the current fast-paced production environment, the demand for creative and effective production techniques is greater than ever. Companies are constantly looking for strategies to cut lead times and costs while upholding quality standards. A technique that has become prominent as a revolutionary approach in this field is fast injection molding. This method allows manufacturers to produce parts quickly and with exceptional accuracy, making it an perfect option for both prototyping and full-scale production.
Rapid injection molding leverages cutting-edge technologies and optimized processes to facilitate quicker turnaround times without compromising on standards. By employing custom fixtures and substances, manufacturers can develop prototypes in a matter of days instead of weeks. This efficiency not only accelerates the goods development process but also improves the ability to adapt to customer demands rapidly. As sectors evolve and customer needs change, rapid injection molding stands out as a crucial approach for ensuring that businesses can deliver prompt and efficient solutions.
Overview of Quick Molding Process
Rapid injection molding is an innovative manufacturing process that greatly reduces the duration required to produce high-quality plastic parts. This process uses fast molds and efficient machinery to manufacture samples and production components at an accelerated pace. By integrating innovative tech with conventional injection molding, manufacturers can streamline their production cycles and adapt more swiftly to consumer demands.
One of the key benefits of quick molding is its ability to accommodate both short and extensive production runs. It enables manufacturers to manufacture resilient and accurate parts that meet rigorous specifications while minimizing costs. This versatility makes it an perfect choice for sectors ranging from car manufacturing to consumer electronics, where time-to-market is critical. The technique can swiftly shift from initial model to completed product without compromising quality.
Furthermore, rapid injection molding promotes iterative design and optimization. Engineers can quickly assess different blueprints and materials, gaining critical insights into how modifications affect functionality. This ability not only promotes innovation but also boosts the overall effectiveness of the design process, ultimately leading to better-end products that meet customer demands and expectations.
Advantages of Streamlined Design
Efficient design plays a key role in the outcome of product development. By using rapid injection molding, manufacturers can enhance their design processes, allowing for faster iterations and improvements. This rapidity enables designers to quickly test and refine their ideas, ultimately leading to more effective products. The ability to rapidly generate top-notch prototypes not only hastens the design phase but also helps teams identify potential issues early in the process.
Another important benefit of streamlined design lies in financial efficiency. Rapid injection molding lowers the time spent on each production cycle, which translates into lower labor and overhead costs. Additionally, the exactness of this method reduces material waste, contributing to more green manufacturing practices. By optimizing designs for ease of production, companies can achieve financial savings and ultimately boost their profit margins while delivering high-quality products to the market.
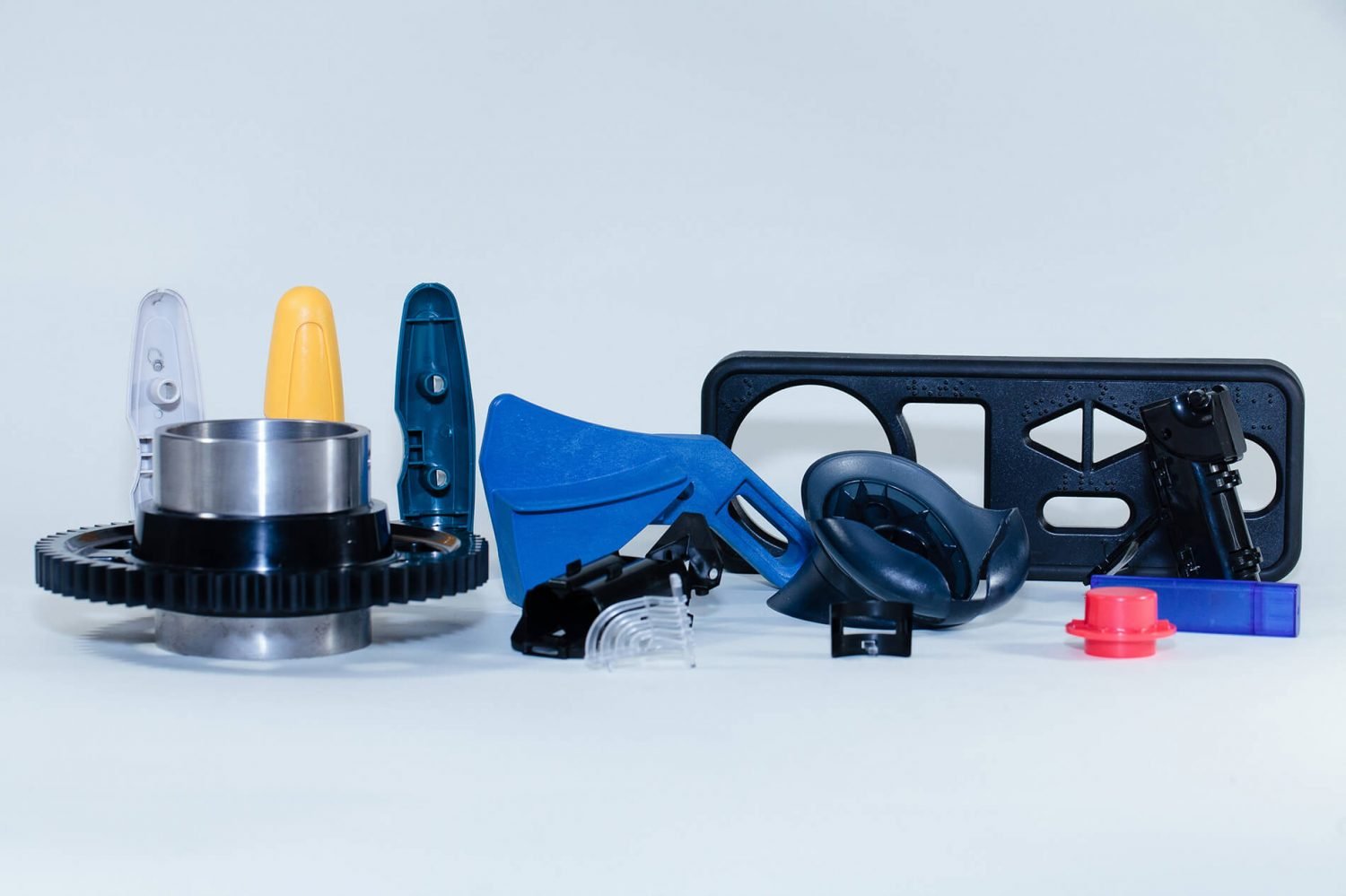
Moreover, effective design fosters progress. When designers are released from the constraints of longer lead times and high costs, they are encouraged to explore unique solutions. With rapid injection molding, manufacturers can experiment with diverse materials and complex geometries that may not have been possible with traditional methods. This innovation not only upgrades the product offerings but also positions companies as front-runners in their respective industries, driving competitive advantages in a rapidly changing market.
Applications and Prospective Trends
Accelerated injection molding is on the rise across different sectors due to its potential to reduce delivery times and manufacturing costs. In the car industry, companies are more and more utilizing this technique to create complex parts quickly, enabling for speedier prototyping and adaptation to designs modifications. By employing this technology, factories can construct intricate shapes that are critical for boosting vehicle performance and efficiency, while also fulfilling the growing need for customization.
The medical field also receives substantially from accelerated injection molding, particularly in the manufacturing of custom devices and components. This method allows the creation of precision parts that meet stringent regulatory requirements while keeping cost-effectiveness. As the demand for tailored healthcare and bioengineering rises, rapid injection molding is ready to play a significant role in supplying high-quality medical devices tailored to individual patient needs.
Looking ahead, the outlook of rapid injection molding appears promising with advancements in materials and tech. The incorporation of intelligent production techniques, such as automation and artificial intelligence, will enhance the efficiency of the process, leading to quicker production cycles and more design versatility. As sustainability becomes a priority, new sustainable materials for rapid injection molding will probably emerge, aiding manufacturers in their pursuit of eco-friendly production methods.